Interior vehículo
Aplicaciónes > ► Automotriz > ► Interior vehículo
¿Qué es el habitáculo de un vehículo?
Todos los interiores de automóviles, incluidos los componentes de los instrumentos, las superficies interiores, los paneles del salpicadero, los tiradores de las puertas, las guanteras, las rejillas de ventilación, los revestimientos del techo, los paneles de instrumentos, los tiradores de las puertas, las consolas centrales y los compartimentos del salpicadero son ejemplos de productos moldeados por inyección. Además, todos los moldes decorativos para automóviles de lujo se fabrican también con la misma tecnología de fabricación El habitáculo de un vehículo es el espacio interior donde se ubican los asientos, los controles para la conducción, así como otros dispositivos de confort y seguridad. Es la zona central del vehículo, diseñada para proteger a los pasajeros y facilitar la conducción El habitáculo de un coche está compuesto por diversos elementos que en conjunto proporcionan seguridad y comodidad. Algunos de los principales componentes son:
- Asientos: Están diseñados para brindar soporte y confort a los ocupantes. Los asientos a menudo cuentan con ajustes para adaptarse a las diferentes necesidades de los pasajeros y pueden incluir funciones como calefacción o ventilación
- Sistemas de seguridad: Incluyen cinturones de seguridad y airbags, diseñados para proteger a los ocupantes en caso de colisión, actuando a compresión y disipando la energía del impacto
- Volante y pedales: Son esenciales para la conducción y permiten al conductor controlar el vehículo con precisión
- Panel de instrumentos: Proporciona información vital sobre el estado del vehículo al conductor, ayudando a mantener la seguridad en el camino
- Sistemas de climatización y entretenimiento: Añaden confort y funcionalidad, haciendo de cada viaje una experiencia más agradable
Interior del vehículo
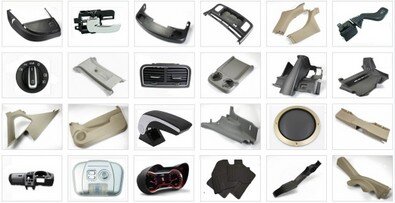
- Temperaturas: debajo de las ventanas hasta 80°C
- Ventana y superior hasta 90°C
- Bandeja para bandas y paquetes hasta 125°C
(A una temperatura ambiente de 40°C y la luz solar directa, estas altas temperaturas locales debajo de las pantallas delanteras y traseras realmente ocurren, con las pantallas modernas 'aerodinámicas' de ángulo bajo. Por lo tanto, los problemas de deformación son más urgentes con las fascias y los estantes para paquetes).
- Productos químicos: Líquidos de limpieza y detergentes: cosméticos, comida y bebida, sudor,derrames.
- La resistencia a los rayos UV sigue siendo relevante para las piezas interiores.
Tradicionalmente, los paneles de instrumentos (IP) se fabricaban con varios componentes metálicos que debían pintarse y se mantenían unidos por una estructura de soporte de acero. Los plásticos ingresaron inicialmente al mercado IP para mejorar la estética sobre la estructura de acero. Con el paso del tiempo, los termoplásticos se han expandido aún más en este segmento de aplicaciones, lo que facilita diseños complejos y una reducción tanto en el costo como en el peso. Estos termoplásticos incluyen lo siguiente: • Acrilonitrilo-butadieno-estireno (ABS) • ABS de alta temperatura (HHABS) • Mezclas de policarbonato (PC) y ABS • Éter de polifenileno modificado (PPE) • Polipropileno modificado (poliolefina termoplástica [TPO]) • Polipropileno con fibra de vidrio larga (LGF PP) y ABS • Anhídrido maleico de estireno (SMA).
Moda y funcionalidad
Sin duda, en el competitivo mercado actual, el habitáculo es una de las principales características de venta del vehículo. (Esto es igualmente cierto en el sector comercial de la industria). No es necesario ser psicólogo para reconocer que el atractivo de las ventas se registra en dos niveles: como "cabina de mando" y como" espacio vital". La cabina exige una satisfactoria sofisticación y complejidad de funciones, exhibidas de manera accesible y atractiva; el espacio habitable debe proporcionar comodidad y cuidado para el conductor y los pasajeros. Todo estilista sabe que hay elementos funcionales y de moda en el diseño de cada componente. La gran contribución de los plásticos ha sido ofrecer libertad de diseño, permitiendo al estilista atender ambos elementos. Para las superficies interiores, ahora se ofrecen muchas opciones:
- Superficies duras o blandas
- Aspecto mate o brillante
- Acabado liso o texturizado
- Color en profundidad o superficie pintada
Más allá de estas consideraciones, existe una libertad de forma prácticamente completa. Sobre todo, existe la posibilidad de integrar componentes, consolidarlos en una mejor forma con una función mejorada, y todo ello con menores costes de montaje. Para una producción de alto volumen, el proceso de moldeo por inyección es el más efectivo para lograr bajos costos unitarios. Las ventajas de la producción en masa se pueden combinar con las necesidades de un mercado fragmentado y personalizado mediante sistemas de diseño modular, lo que permite producir varios conjuntos diferentes a partir de unas pocas herramientas racionalizadas. Las espumas plásticas amplían enormemente la libertad de diseño del estilista. Funcionalmente, son la base del aislamiento acústico y vibratorio, y pueden hacer una gran contribución a la seguridad de los pasajeros. Los avances en la espuma de poliuretano han sido cruciales para mejorar los diseños y la eficiencia de producción en los asientos de automóviles modernos.
Componentes interiores
Los componentes interiores de un vehículo consisten principalmente en IP, paneles de puertas y asientos; en conjunto, representan la mayor parte de los plásticos en un automóvil con un 38%. Se espera que estos componentes satisfagan principalmente los requisitos de comodidad, olor, atractivo estético, diseño ergonómico y durabilidad. Por ejemplo, la mayoría de los paneles interiores deben tener un acabado Clase A. Desde una perspectiva de seguridad, todos los materiales utilizados para fabricar componentes interiores deben cumplir con la Norma Federal de Seguridad de Vehículos Motorizados (FMVSS) No.302, titulada "Inflamabilidad de los materiales interiores". Según esta norma, el material no debe arder ni transmitir un frente de llama a través de su superficie a una velocidad superior a 4 pulg/min. La característica crucial de la cual fue la prueba de impacto de la cabeza en el panel de instrumentos. Más recientemente, la legislación de protección de los ocupantes se ha vuelto mucho más exigente y especificaciones como FMVSS 208 presentan una amplia selección de requisitos como los siguientes:
- Colapsabilidad de la columna de dirección
- Pruebas de impacto de cabeza en panel de instrumentos y molduras de pilares
- Prueba de impacto de rodilla en ciertas áreas del panel de instrumentos
- Prueba de impacto corporal en los respaldos de los asientos
- Ensayos de impacto lateral contra puertas y molduras laterales
Además, los componentes interiores también deben poseer propiedades de empañamiento y acústicas. A continuación se ofrece una descripción detallada de los plásticos utilizados para componentes interiores importantes. Hoy en día, los componentes interiores representan la mayor proporción de plásticos en los vehículos. No se espera que este hecho cambie drásticamente a medida que los plásticos continúen ganando aceptación para su uso en otros lugares en los vehículos. Tradicionalmente, los paneles de instrumentos (IP) estaban hechos de varios componentes metálicos que tenían que pintarse y se mantenían unidos por una estructura de soporte de acero. Los plásticos ingresaron inicialmente al mercado de la propiedad intelectual para mejorar la estética en la parte superior de la estructura de acero. Con el paso del tiempo, los termoplásticos se han expandido aún más en este segmento de aplicaciones, facilitando diseños complejos y una reducción tanto en el costo como en el peso. Estos termoplásticos incluyen los siguientes:
• Acrilonitrilo-butadieno-estireno (ABS)
• ABS de alta temperatura (HHABS)
• Mezclas de policarbonato (PC) y ABS
• Polifenileno éter modificado (PPE)
• Polipropileno modificado (poliolefina termoplástica [TPO])
• Polipropileno con relleno de vidrio largo (LGF PP) y ABS
• Anhídrido maleico de estireno (SMA)
Los factores que afectan la selección del material para aplicaciones interiores incluyen: • costo • estética • ajuste • acabado • acústica • propiedades mecánicas • estabilidad dimensional • resistencia al calor • unión adhesiva • colorabilidad • procesabilidad. Dos de las aplicaciones más comunes de los PAB son paneles de instrumentos y consolas, molduras, pilares, etc. Cada una de estas categorías presenta problemas especiales para los diseñadores de materiales: Paneles de instrumentos: • costo • seguridad (rodilleras, gestión de la energía) • estilismo • resistencia a la temperatura • consolidación de piezas. Consolas, paneles, pilares, molduras de puertas: • costo • funciones de calidad • resistencia al calor • estabilidad dimensional. Las aleaciones de ABS/PP tienen una alta aceptabilidad en aplicaciones automotrices porque sus componentes principales ya se utilizan ampliamente para aplicaciones interiores, por lo que no introducen ningún componente nuevo en el flujo de reciclaje. Así, el suministro de aleación ABS/PP se derivaría parcialmente de la chatarra interior reciclada que ha sido mezclada y compatibilizada en una extrusión reactiva. Probablemente se agregarían materiales vírgenes para mejorar el rendimiento. El precio es fundamental, lo que puede limitar las opciones de compatibilización, lo cual no es sencillo. Una de las aleaciones más utilizadas en el interior de los automóviles es el PC/ABS. El cambio del material típico, ABS, a PC/ABS se debe a la necesidad de una mayor capacidad térmica y una mayor resistencia al impacto. También hay un cambio de PC que se usa tradicionalmente en áreas que requieren alto impacto, a PC/ABS, por razones de flujo de fusión mejorado. En este caso, la aleación PC/ABS también proporciona una resistencia química mejorada, especialmente a los hidrocarburos, que es de gran importancia en entornos de automoción. Además, se logra una resistencia al impacto mejorada en geometrías de piezas de sección transversal grande donde se sabe que la PC es deficiente. Un uso especial de los PAB en los componentes interiores es el panel de instrumentos (IP). El IP es único en el automóvil, primero por su ubicación, donde puede ser calentado por el sol hasta temperaturas superiores a 120°C. En segundo lugar, es único debido a la gran carga de componentes adjuntos. Por último, y quizás lo más importante, es único debido a los requisitos de impacto extremo. Los parámetros de diseño pueden superar los requisitos de rendimiento de los materiales típicos que se utilizan, como SMA reforzado con vidrio o PPE/PS reforzado con vidrio. Se necesita refuerzo de vidrio para lograr la alta rigidez (módulo de elasticidad> 5,2 GPa) necesaria para mantener la estabilidad de la pieza en todo el tramo del ancho del vehículo, típicamente hasta 2 m. Las piezas de ese tamaño requieren una atención estricta al diseño de las herramientas de moldeo por inyección, especialmente la compuerta y la posición de las líneas de soldadura. Hay una multitud de piezas expuestas unidas al retenedor de IP que, en caso de accidente, es probable que golpeen a un ocupante. Son motivo de gran preocupación las rodilleras y la guantera, que probablemente sean puntos de impacto en las rodillas de los ocupantes. Para la resistencia al impacto, el requisito de rendimiento es la retención de suficiente tenacidad a baja temperatura, es decir, de -30 a -40°C. A temperaturas tan bajas, la presencia de PC en mezclas de PC/ABS ayuda a aumentar el impacto por encima del ABS solo. Otra razón por la que se utilizan aleaciones basadas en PC en los interiores de los automóviles es la resistencia química mejorada sobre los estirénicos, como el ABS. En el sistema IP, la resistencia al impacto y al agrietamiento es necesaria para todos los componentes. Todo el conjunto se prueba en varias configuraciones de impacto simulado a temperaturas tan bajas como -40°C. El PC/ABS tiene un rendimiento significativamente mejor que el ABS y se ha descubierto que es más duradero que el PC en el entorno del automóvil. También es fundamental la capacidad del IP para resistir las fuerzas del despliegue de la bolsa de aire sin romperse o deformarse permanente inaceptable o dañar otros componentes. La tendencia en la industria es hacia IP de alto módulo. La alta rigidez se correlaciona con una mayor frecuencia de resonancia y características superiores de ruido, vibración y dureza (NVH). A medida que los fabricantes de automóviles agregan más componentes a la IP, como sistemas de música, teléfonos y sistemas de navegación, se debe aumentar la capacidad de carga de toda la estructura de IP, mientras se mantiene la resistencia para resistir los impactos del despliegue de las bolsas de aire y los choques. En comparación con los materiales monolíticos convencionales, como PP y ABS, en muchas de las aplicaciones IP, el cambio a PC/ABS y PPE/PS aumenta la capacidad térmica y la resistencia al impacto. La incorporación de poliésteres en aplicaciones de interior se debe en gran medida a su compatibilidad con otros materiales del automóvil, como tapizados y alfombras. A medida que el reciclaje se vuelve cada vez más importante, indudablemente avanzarán las tendencias hacia el uso de materiales compatibles como estos. Las aleaciones a base de poliéster se pueden formular con el equilibrio de propiedades deseado necesario para el moldeado y el rendimiento en las piezas interiores. La menor viscosidad del componente cristalino de la aleación proporciona características de flujo mejoradas y la capacidad de reproducir bien la textura de la superficie del molde, especialmente cuando es deseable un brillo bajo. El reemplazo de ABS por PC/ABS para aplicaciones de interior en los últimos años se debe en parte a la reducción del brillo. Los materiales de flujo fácil o alto son importantes para aplicaciones en las que las piezas pueden ser grandes, requiriendo inyección de múltiples compuertas, y es deseable una buena apariencia en las líneas de soldadura para eliminar la pintura. Cuando se va a eliminar la pintura, es necesaria la estabilidad a los rayos UV. Para mezclas que contienen ABS, la porción de butadieno del ABS tiende a degradarse con el tiempo, por lo que el aspecto de la superficie y la dureza sufren. Por esta razón, las mezclas de PC/ASA están experimentando un mayor uso tanto para aplicaciones interiores como exteriores. El único inconveniente de las aleaciones en estas aplicaciones, donde no son necesarias altas temperaturas o impactos, es el costo, que suele ser más alto que el ABS o el PP. Otros sistemas de materiales se están utilizando cada vez más. Se utiliza una mezcla de SMA y HIPS en las piezas del tablero de automóviles. Las mezclas de PVC/ABS se utilizan para el moldeado en polvo de pieles IP. Para aplicaciones interiores en el transporte público, otra mezcla ha ganado un uso generalizado: las piezas de acrílico/PVC fabricadas mediante termoformado. Sus láminas extruidas se utilizan como bancos, respaldos de asientos, reposabrazos y revelaciones de ventanas para subterráneos, vagones de ferrocarril, autobuses, monorraíles y carros. Las propiedades clave que posee esta aleación incluyen la resistencia al rayado y al rayado, y la capacidad de limpiarse fácilmente con detergentes fuertes.
Tipos de plásticos
Los diseños que utilizan termoplásticos podrían permitir la integración de carcasas de airbag, carcasas de instrumentos, etc., con necesidades estructurales (es decir, partes estructurales de IP), lo que permite para la eliminación de vigas de acero. Sin embargo, las ventajas de costes siguen siendo discutibles. Echemos un vistazo más de cerca a algunos de los plásticos en aplicaciones interiores y sus características de rendimiento. Debido a su útil combinación de tenacidad, rigidez, resistencia a los disolventes y procesabilidad, los polímeros ABS comenzaron a aparecer en aplicaciones de interior durante la década de 1980. Estos materiales se crean mediante la polimerización de acrilonitrilo, butadieno y estireno. La cantidad de cada uno de estos tres monómeros juega un papel importante en las propiedades finales del copolímero resultante. Los proveedores de resinas pueden adaptar las resinas para aplicaciones y mercados particulares variando las proporciones de estos tres monómeros y las morfologías de las fases dispersas en el procesamiento posterior. La reciente introducción de poliolefina termoplástica (TPO) en el mismo espacio de aplicación ha supuesto un desafío considerable para los proveedores de ABS en términos de mejora del brillo. Aunque el ABS tiene mejores propiedades mecánicas que la mayoría de los TPO compuestos, el menor brillo del TPO ofrece el beneficio de las piezas moldeadas en color para que las utilicen los fabricantes y, en última instancia, los fabricantes de equipos originales (OEM). Recientemente, algunos fabricantes afirman haber reducido el brillo del ABS al nivel de TPO ajustando la morfología, pero la aceptación comercial de tales materiales se encuentra solo en una etapa inicial. El brillo del grado de ABS tal como se moldearon son sin duda mejores que los de un TPO competitivo considerado la aplicación específica. La necesidad de equilibrar la rigidez y la tenacidad superiores a las del ABS existente llevó a la introducción de mezclas de PC/ABS en la industria automotriz. Las mezclas de polímeros siempre han jugado un papel importante en las aplicaciones automotrices al proporcionar propiedades adicionales que no se pueden lograr con un solo material. Debido a su versatilidad, las mezclas de PC/ABS se consideran un material de ingeniería fundamental para aplicaciones como IP de automoción y paneles de carrocería. Aunque el ABS y el PC son resinas amorfas extremadamente útiles, tienen algunas limitaciones que solo pueden resolverse usándolas como mezclas. Por ejemplo, la PC ofrece una claridad, dureza y resistencia al calor excepcionales. Asimismo, es sensible a las muescas y es más difícil de procesar que las resinas ABS. Del mismo modo, el ABS es un material resistente, se procesa fácilmente y se adhiere bien a la pintura y las espumas. Debido a la compatibilidad excepcional entre estas fases, una aleación de estas dos resinas da como resultado una resina con una combinación única de sus propiedades. Las mezclas de PC y ABS se destacan por ofrecer alta resistencia al calor, rigidez, alto impacto, tenacidad con menos sensibilidad a las muescas, procesabilidad mejorada y características de superficie versátiles.
El impacto Izod con muescas es óptimo cerca del 70% del peso de PC en la composición de la mezcla (o 65% PC y 35% ABS por peso). La mayoría de las mezclas de PC/ABS que se venden en el mercado hoy en día están formuladas a partir de la composición de mezcla óptima. Estas mezclas de PC/ABS están disponibles en cuatro grados, según las necesidades de rendimiento:
- Uso general
- Alto flujo
- Moldeo por soplado
- Bajo brillo
Los cuatro grados se formulan incorporando rellenos minerales, fibras de vidrio, fibras de carbono, etc. adelante para satisfacer la necesidad de rendimiento para aplicaciones rígidas con muy poco sacrificio de tenacidad. El éter de polifenileno modificado (PPE), más exactamente llamado poli (éter de 2,6-dimetil-p-fenileno), se obtiene mediante la oxidación de fenoles sustituidos. Se caracteriza por grupos de fenilos regulares y muy espaciados. (El fenol es un compuesto químico aromático derivado del benceno). General Electric Plastics hizo que este polímero estuviera disponible comercialmente como óxido de polifenileno (PPO). A menudo se modifica mezclándolo con un segundo polímero que generalmente es un poliestireno (PS). Este polímero de alto rendimiento ofrece altas temperaturas de deflexión por calor y buena resistencia a las llamas, y proporciona una buena resistencia al flujo y al impacto solo cuando se combina con poliestireno de alto impacto. Sin embargo, la falta de resistencia química, resistencia a los rayos ultravioleta (UV) y estabilidad del color significa que los artículos hechos de este polímero deben pintarse con frecuencia cuando se utilizan en algunas aplicaciones interiores exigentes. Para los IP, la resistencia a los rayos UV y la estabilidad del color son críticas y, a menudo, se prefieren a la alta resistencia al calor (por ejemplo, valores de resistencia al calor de aproximadamente 208°C para PPE, en comparación con aproximadamente 145°C para PC e incluso más bajos para ABS de uso general ). Este polímero también se mezcla con nailon y se comercializa con el nombre de Noryl. Las medias de nailon son un tipo de los primeros polímeros desarrollados por Carothers en la década de 1930. La mayoría de las medias de nailon se sintetizan agregando repetidamente dos moléculas de una diamina y dos moléculas de un ácido. Dependiendo del tipo de molécula, el nailon puede tener una amplia gama de propiedades. La poliolefina termoplástica es una mezcla polimérica útil de polipropileno (PP), relleno, aditivos (por ejemplo, agentes deslizantes y antioxidantes) y un elastómero termoplástico. En general, el TPO se puede clasificar en dos categorías amplias:
- Alta rigidez
- Alta tenacidad
En la actualidad, los TPO se utilizan cada vez más en aplicaciones automotrices especiales debido a su menor gravedad específica, moldeabilidad por inyección, economía, reciclabilidad y rendimiento de ruido. Algunas variaciones de estos ingredientes esenciales se combinan en extrusoras (otros mezcladores) o se preparan en alguna combinación de reactores (a menudo denominados reactor TPO) que pueden producir tanto PP como el caucho, seguido de alguna adición posterior al reactor de otros productos químicos. La proporción de elastómero a PP en esta mezcla se puede ajustar para controlar el módulo y la recuperación elástica de un TPO. Como ya se indicó, las formulaciones típicas de TPO se pueden clasificar para aplicaciones de alta rigidez y alta tenacidad (módulo bajo). Las formulaciones de tenacidad están diseñadas para una temperatura de transición de dúctil a frágil (DBTT) baja de –40°C medida por una prueba de impacto Izod con muescas (método de prueba ASTM D265), mientras que las formulaciones de alta rigidez están en el rango de –20°C. El módulo de moldura de puerta combina todos los componentes de hardware de la puerta más el panel de moldura. Fue moldeado por inyección por utilizando un grado específico de TPO. El PP y el ABS con relleno de vidrio largo (LGF) son mezclas reforzadas con vidrio de PP y ABS. Se estima que aproximadamente el 30% de los 2 millones de toneladas métricas de fibra de vidrio electrónico que se consumen a nivel mundial para el refuerzo de polímeros se utiliza en compuestos termoplásticos. (El vidrio E es un tipo de vidrio libre de álcalis que se utilizó originalmente en aplicaciones eléctricas).
Estos compuestos han estado creciendo a un ritmo saludable del 15 al 20% por año, en gran parte impulsados por aplicaciones automotrices. Dos razones clave por las que los termoplásticos reforzados con vidrio se están volviendo tan importantes son su reciclabilidad y su adecuación al proceso de moldeo por inyección. La incorporación de refuerzo LGF en PP ha facilitado el uso de un polímero de menor costo en aplicaciones de ingeniería semiestructural en la industria automotriz. Además, LGF PP es especialmente interesante porque las capacidades de refuerzo mejoradas de la fibra de vidrio y el costo y rendimiento del PP lo convierten en un material de ingeniería económico. Este material está ganando importancia rápidamente, como lo demuestra su tasa de crecimiento anual de más del 35% en los últimos cuatro años. Aunque es menos versátil que LGF PP, LGF ABS se introdujo recientemente y promete un mejor equilibrio en el rendimiento de impacto. Otro plástico llamado anhídrido maleico de estireno (SMA) se introdujo comercialmente por primera ven 1960 y se vende también para el segmento del mercado de propiedad intelectual. Los copolímeros de estireno anhídrido maleico se desarrollaron a fines de la década de 1960. A principios de la década de 1970, los grados de reactor modificado con elastómero y reforzado con fibra de vidrio ofrecían una mayor resistencia al calor, resistencia al impacto, resistencia a la tracción y flexión, y propiedades de módulo de flexión. Estas características de rendimiento se adaptaron a una aplicación automotriz nueva y en crecimiento: sustratos moldeados por inyección para IP blandas. A fines de la década de 1970, los diseños de vehículos aumentaron la pendiente del parabrisas, lo que a su vez aumentó la temperatura en la superficie superior de los IP expuestos. Debido a la expansión térmica de la viga transversal del automóvil, los IP que usaban sustratos de la competencia se doblaban y deformaban a lo largo del borde del parabrisas. La estabilidad térmica de las resinas reforzadas con vidrio demostró las propiedades físicas necesarias para resistir la expansión térmica en los nuevos diseños. reforzado con vidrio también se reunió con U.S. regulaciones gubernamentales para mejorar la seguridad y el impacto en la cabeza mediante una mayor gestión de la energía en un rango de temperaturas y velocidades. Los IP suaves progresaron más allá de los soportes de la espuma de poliuretano para incluir diseños más intrincados para construcciones IP de una y dos piezas. Los nuevos diseños eran más funcionales, tenían una estructura cruzada mejorada y contenían compartimentos de embalaje adicionales para las aberturas de la radio, el calentador y el velocímetro. Las variaciones de termoplásticos formulados discutidas hasta ahora se pueden utilizar en cualquier aplicación de molduras blandas o duras, cajas de guantes y bandejas de embalaje. Los tapetes son paneles que se colocan entre el motor y el panel de instrumentos para evitar que el ruido del motor y otros ruidos del aire lleguen a los oídos de los ocupantes de un automóvil. En los últimos años, el TPO relleno se ha formulado para funcionar como una barrera de sonido con varios absorbentes de sonido porosos. Los termoendurecibles rígidos de poliuretano (PU) también se pueden utilizar como soluciones para tapetes. Los techos, otro componente del segmento interior, constan de muchas partes funcionales debajo del techo, y la PU rígida se usa con mayor frecuencia como respaldo para las espumas y telas subyacentes. Las soluciones termoplásticas se encuentran con menos frecuencia en esta aplicación. Los plásticos se han utilizado recientemente en los respaldos de los asientos mediante una considerable modificación de ingeniería de diseño. Un impulso hacia la reducción de peso hizo posible este cambio, y un número cada vez mayor de OEM están reconociendo la ventaja de los plásticos en esta aplicación. Los respaldos de los asientos son un elemento de seguridad altamente regulado, se introdujo por primera vez los plásticos en 2000 para su uso en los respaldos de los asientos traseros. Tradicionalmente, el acero ha sido el material de elección. Sin embargo, la introducción de PC/ABS como una estructura moldeada por soplado de doble carcasa condujo a un ahorro de peso del 20 al 25 %. Esta mezcla se introdujo por primera vez con éxito en el 2006 en Europa. Posteriormente, otros fabricantes de equipos originales de América del Norte adoptaron diseños de respaldo de asiento similares hechos de PC/ABS para vehículos grandes, pero TPO o TPO reforzado también podrían usarse en esta aplicación.
Las bases de los asientos son más exigentes que los respaldos. Deben proporcionar resistencia a la fluencia a largo plazo y deben soportar choques a baja velocidad. También deben poder acomodar varias características de comodidad (por ejemplo, sistema de reclinación, calefacción y masaje). Para los automóviles de alta gama, la necesidad de rendimiento a menudo impulsa la elección del compuesto de polímero (es decir, termoplástico o termoestable). Para automóviles de gama baja, los tipos de soluciones termoplásticas LGF pueden ser adecuadas. Recientemente, los fabricantes han intentado introducir un asiento de una pieza con características de reclinación opcionales que serían adecuadas para automóviles de bajo costo. Los ingenieros están tratando de hacer asientos más delgados y livianos para mejorar la eficiencia del combustible, pero los plásticos aún no han aparecido como el principal candidato.10 Las manijas de las puertas interiores son menos exigentes que las manijas de las puertas exteriores en términos de resistencia química. Claramente, PC / ABS es un ganador en esta aplicación. Los volantes están hechos de resinas de éster de vinilo moldeadas y pigmentadas o de uretano pigmentado moldeado por inyección por reacción (RIM) cuando se requiere un material dúctil. El acetilo de baja fricción se usa a menudo para los interruptores, palancas y cojinetes de las columnas de dirección. También se utiliza en una variedad de aplicaciones automotrices debido a su capacidad para soportar altas tensiones mecánicas y térmicas. Hay dos tipos de resinas de éster de vinilo:
- Resinas a base de epoxi
- Resinas sin base de epoxi
Un éster de vinilo sin base de epoxi es simplemente un poliéster terminado en metacrilato. Tiene una resistencia reducida a cáusticos y ácidos y se puede utilizar como resina aglutinante compuesta de plástico en aplicaciones donde la alta resistencia química no es crítica. Las resinas epoxi viniléster no han penetrado en el mercado automotriz porque los poliésteres relativamente económicos pueden satisfacer la mayoría de las necesidades de desempeño, excepto la resistencia química. Sin embargo, es posible imaginar la introducción de resinas epoxi de éster vinílico en aplicaciones más corrosivas o severas cerca del motor, baterías, partes externas del cuerpo, etc. El PU moldeado por reacción-inyección ofrece una solución para la producción rápida de piezas de plástico complejas directamente a partir de monómeros de baja viscosidad (unidad química única) y oligómeros (cadena de unidades químicas múltiples). La química del PU moldeado por reacción-inyección implica específicamente la mezcla de polioles (oligómeros de unidades de alcohol) e isocianatos (compuestos de carbono-nitrógeno). Se requiere un mezclado minucioso en la fase de mezclado para lograr propiedades físicas uniformes en la pieza final fabricada. Para aplicaciones comerciales, la mayoría de las reacciones químicas de RIM en el molde deben tener lugar en menos de un minuto. Los sistemas RIM PU no reforzados son suaves y elásticos y pueden tener un módulo cercano a 1000 MPa, una resistencia de aproximadamente 30 MPa y un alargamiento promedio a la rotura cercano al 150%. La expansión térmica de los sistemas de PU no reforzados se puede reducir aproximadamente diez veces en los compuestos de PU de RIM mediante el uso de rellenos adecuados. El nailon 6,6 es el principal polímero de los tejidos de las bolsas de aire en la actualidad. Es una solución madura en la que el airbag se recubre con silicona para cumplir con los requisitos de permeabilidad. El policloropreno fue el polímero elegido como recubrimiento en el desarrollo inicial de las bolsas de aire, pero sus defectos inherentes hicieron de la silicona el recubrimiento preferido. Los airbags están cosidos principalmente con hilo de nailon 6,6. Con la consideración de enfoques de despliegue alternativos a la pirotecnia basada en azidas actual y la introducción de más bolsas de aire o cortinas de aire infladas en los vehículos, los nuevos enfoques de materiales serán más factibles. Los copolímeros de bloque de estireno-etileno (SEB) son los principales titulares de las cubiertas de las bolsas de aire. A menudo se les conoce como r-TPV (fabricado mediante un proceso de extrusión reactiva con monómero de etileno propileno dieno [EPDM], un reticulante y PP). La demanda global total de SEBS es de aproximadamente 30 millones de libras, dividida casi en partes iguales entre Japón, América del Norte y Europa. Debido al temor de litigios relacionados con la seguridad, los compuestos de SEBS asociados con las bolsas de aire están diseñados para tener un alargamiento, tracción y resistencia superiores. resistencia al desgarro sobre muchos otros elastómeros termoplásticos. Los SEB son parte de la familia de copolímeros de bloques de estireno (SBC). En un sentido crudo, los SBC poseen propiedades de resistencia que son equivalentes a las de los sistemas de elastómeros vulcanizados sin vulcanización. Así, el interior de los vehículos es una aplicación clave para el uso de plásticos. Estas aplicaciones interiores incluyen IP, paneles de la carrocería y paneles de las puertas, tapetes, respaldos de asientos, bases de asientos, volantes y cubiertas de bolsas de aire. Los materiales que se utilizan hoy en día pueden ser polímeros individuales o mezclas que ofrecen una variedad de propiedades, que incluyen alta resistencia al impacto, alta rigidez, moldeabilidad por inyección y resistencia al calor. A medida que avanza la ciencia de los materiales, se espera que los plásticos desempeñen un papel importante en el interior de los vehículos.
Interior del vehículo
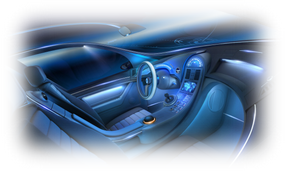
Los fabricantes de equipos originales automotrices (OEM) exigen componentes de la más alta calidad en toda la cadena de suministro. Cada material y componente automotriz debe someterse a pruebas rigurosas y cumplir con los más altos requisitos legales y de la industria. Mexpolimeros ayuda a los fabricantes y proveedores con servicios de prueba independientes asegurados frente a una amplia gama de especificaciones de prueba de OEM, estándares nacionales (BS, ASTM, DIN, JAS) e internacionales (ISO, EN, SAE). Los servicios de prueba de SATRA están acreditados según ISO 17025.
El predominio del plástico
La inspección de cualquier modelo de automóvil muestra que el habitáculo está dominado por los plásticos. Aparte del acristalamiento, prácticamente todas las superficies son producto de la química de los polímeros, ya sea como superficie sólida o como tela. Ésta es el área donde los plásticos están más firmemente establecidos: de hecho, el habitáculo representa alrededor del 56% del uso total de plásticos para automóviles. Sin embargo, el dominio es menos completo de lo que parece. En el habitáculo, los plásticos han hecho incursiones muy pequeñas en las piezas estructurales y mecánicas críticas para la seguridad. La comparación de los automóviles modernos de alto volumen con los de años anteriores, incluso hasta los 1950, demuestra algunas diferencias sorprendentes. El estilo interior hizo pocas concesiones a la comodidad de los pasajeros, o incluso a la seguridad de los pasajeros. En los últimos años, sin embargo, la seguridad ha sido una de las principales influencias. La información obtenida de un catálogo sombrío de estadísticas de accidentes ahora está respaldada dentro de las compañías de motores por programas masivos de pruebas de impacto sofisticadas. con maniquíes extensamente monitoreados. Históricamente, el hito de seguridad más importante para el compartimiento de pasajeros fue el estándar federal estadounidense de seguridad de vehículos motorizados FMVSS 201, cuya característica crucial fue la prueba de impacto de cabeza en el panel de instrumentos. Más recientemente, la legislación de protección de los ocupantes se ha vuelto mucho más exigente y especificaciones como FMVSS 208 presentan una amplia selección de requisitos como los siguientes:
- Columna de dirección colapsable
- Prueba de impacto de cabeza en el panel de instrumentos y molduras de pilares
- Prueba de impacto de rodilla en ciertas áreas del panel de instrumentos
- Prueba de impacto corporal en los respaldos de los asientos
- Ensayos de impacto lateral contra puertas y molduras laterales
Tendencias
Tradicionalmente, el habitáculo es la parte del vehículo que soporta los costes de montaje más elevados. Las ventajas potenciales de los plásticos para facilitar la consolidación de componentes y la construcción modular los hacen, en consecuencia, particularmente atractivos en esta área. El montaje fuera de línea, completo con componentes eléctricos, de subconjuntos sofisticados es una extensión lógica de los beneficios que ofrecen los plásticos. Esta es ahora una tendencia bien establecida. El PVC fue una vez la superficie casi universal en el interior de los automóviles. Aunque sobrevive como sellos y polainas, y como revestimientos de fascia en combinación con ABS y PUR, se ha desplazado en gran medida de los asientos y los paneles de las puertas. La moda actual es por los textiles, principalmente en nylon 66 y poliéster PET. La tendencia se extiende no solo a los asientos (donde los beneficios de 'comodidad' de materiales como el nailon 66 tejido por urdimbre son obvios), sino a los revestimientos de puertas semirrígidos donde la tela cubre una superficie de celulosa resinada o polipropileno. Para estas aplicaciones, se han desarrollado tejidos de poliéster que pueden soportar las temperaturas y presiones del moldeo por inyección sin aplastamiento del pelo. Cada vez más en Europa, la tela se aplica como trilaminado, en el que la tela de la cara está respaldada por una capa de espuma y una tela de forro. Las alfombras se están volviendo más sofisticadas, en línea con las otras superficies, en toda la gama de niveles de acabado, desde fieltros puntiagudos en nailon y poliéster hasta terciopelos con mechones más caros en nailon 66. En muchos casos, el respaldo simple de alfombras de PVC o polvo de polietileno de baja densidad está cediendo. a molduras de espuma de poliuretano más elaboradas que proporcionan amortiguación acústica. Las tendencias de estilo aerodinámico están prescribiendo el uso casi universal de parabrisas y ventanas traseras muy inclinadas. Los efectos adicionales de la temperatura y los rayos ultravioleta están imponiendo un módulo y una distorsión térmica muy exigentes. Plásticos en las especificaciones de la industria automotriz sobre los materiales para paneles de instrumentos y estantes para paquetes, y sobre la estabilidad del color de las superficies plásticas y textiles. Moda y funcionalidad Sin duda, en el competitivo mercado actual, el habitáculo es una de las principales características de venta del vehículo. (Esto es igualmente cierto en el sector comercial de la industria). No es necesario ser psicólogo para reconocer que el atractivo de las ventas se registra en dos niveles: como "cabina" y como "espacio vital". La cabina exige una satisfactoria sofisticación y complejidad de funciones, exhibidas de forma accesible y atractiva; el espacio habitable debe proporcionar comodidad y cuidados para el conductor y los pasajeros. Todo estilista sabe que hay elementos funcionales y de moda en el diseño de cada componente. La gran contribución de los plásticos ha sido ofrecer libertad de diseño, permitiendo al estilista atender ambos elementos. Para las superficies interiores, ahora se ofrecen muchas opciones:
- Superficies duras o blandas
- Aspecto mate o brillante
- Acabado liso o texturizado
- Color en profundidad o superficie pintada
Más allá de estas consideraciones, existe una libertad de forma prácticamente completa. Sobre todo, existe la posibilidad de integrar componentes, consolidarlos en una mejor forma con una función mejorada, y todo ello con menores costes de montaje. Para una producción de alto volumen, el proceso de moldeo por inyección es el más efectivo para lograr bajos costos unitarios. Las ventajas de la producción en masa se pueden combinar con las necesidades de un mercado fragmentado y personalizado mediante sistemas de diseño modular, lo que permite producir varios conjuntos diferentes a partir de unas pocas herramientas racionalizadas. Las espumas plásticas amplían enormemente la libertad de diseño del estilista. Funcionalmente, son la base del aislamiento acústico y vibratorio, y pueden hacer una gran contribución a la seguridad de los pasajeros. Los avances en la espuma de poliuretano han sido cruciales para mejorar los diseños y la eficiencia de producción en los asientos de automóviles modernos. El concepto de ensamblajes sándwich abre un abanico de posibilidades muy amplio, utilizando combinaciones de espumas y textiles con pieles y sustratos sólidos. La siguiente sección analiza las características y problemas específicos de los plásticos como superficies, a diferencia de los plásticos como estructuras.
Superficies de plastico
Cualquier panel interior tendrá una función estructural o al menos de soporte, así como cosmética. Sin embargo, es la superficie la principal característica de venta y, por lo tanto, una imperfección de la superficie debe tomarse en serio, incluso si no influye en el funcionamiento del panel.
Tipos de problemas
Entre los posibles problemas con las superficies de plástico se encuentran:
(Todas las superficies)
- Resistencia a la luz
- Resistencia química
- Tinción
- Resistencia a la abrasión
- Distorsión por calor
- Inflamabilidad
- Empañamiento
(Superficies duras)
- Cambios dimensionales
- Ruido
- Distorsión
(Superficies blandas)
- Resistencia al desgarro
- Olor
Los problemas comunes de la resistencia a la abrasión y de la resistencia química y las manchas se han abordado eficazmente en los materiales ahora establecidos en los interiores de los automóviles. Lo mismo puede decirse de la inflamabilidad, siempre que se consideren adecuados los criterios actuales basados en la velocidad de ignición y la propagación de la llama. Los ángulos del parabrisas cada vez más severos están elevando los requisitos de rendimiento en términos de resistencia a la temperatura y la radiación ultravioleta. Los materiales para el panel de instrumentos ahora deben poder soportar una temperatura estática de 125°C. El efecto del aumento de la actividad UV no es cuantificable, pero implica un mayor riesgo de inestabilidad y decoloración del color, e incluso deterioro mecánico. Guarnecido duro Las superficies rígidas que se encuentran con mayor frecuencia en los interiores de los automóviles se basan en ABS y polipropileno. El ABS se ha establecido durante mucho tiempo en molduras duras en virtud de su tenacidad, rigidez y resistencia al rayado, su rendimiento dimensional confiable basado en su baja contracción del molde y su agradable apariencia de brillo medio. El polipropileno se vio por primera vez en interiores a principios de la década de 1960 en forma de paneles decorativos con textura contorneada ("grano de cuero"). La distorsión a la que el polipropileno era propenso en áreas grandes o molduras largas podía disimularse en una forma muy contorneada, y podía obtenerse un efecto mate uniforme en superficies texturizadas más fácilmente que con ABS. En los últimos años, los grados de polipropileno de "reología controlada" (CR), en los que se consigue una contracción más baja y uniforme al reducir la distribución del peso molecular. se han vuelto ampliamente disponibles. Estos polímeros, formulados en una amplia gama de características de rigidez/tenacidad, tienen una distorsión muy reducida, la principal limitación técnica del polipropileno en esta aplicación. Con acabados de textura mate muy de moda y con un ahorro de costes de hasta un 20%, el polipropileno ha desplazado al ABS de gran parte de este sector. Sin embargo, el ABS todavía se prefiere para muchas piezas sensibles a la apariencia y de importancia dimensional, particularmente en formulaciones mates. A un precio ligeramente más alto, las mezclas de PC/ABS ofrecen una mejor combinación de resistencia a la distorsión por calor y estabilidad dimensional que ABS o PP. El poliuretano proporciona una solución para la producción de bajo volumen de superficies rígidas, en forma de llanta reforzada. Una innovación reciente es el uso de plaquitas de vidrio en lugar de fibras, lo que proporciona paneles rígidos con un acabado superficial superior. Structural RIM amplía aún más la versatilidad de PUR: ligeramente reforzado, es adecuado para paneles semirrígidos y, con un refuerzo más pesado, puede usarse para estructuras clave como armaduras de paneles de instrumentos.
Tapizado suave
La tela de cuero a base de pasta de PVC se introdujo como cubierta de asiento en los autobuses de Londres ya en 1941. Morris Motors comenzó a usar tela recubierta de PVC para los asientos en 1944, y los primeros autos producidos en gran volumen hicieron un uso muy extenso de PVC para casi todos los interiores. superficies. En comparación con el cuero, el costo de los materiales y la facilidad de producción resultaron argumentos incontestables. Sin embargo, los vinilos nunca fueron una opción popular para las superficies de los asientos, y el desarrollo de telas de nailon y poliéster tejidas y tejidas mejoradas inició el proceso de sustitución del PVC durante la década de 1960. La introducción de nuevas variaciones de láminas de PVC perforadas y texturizadas no logró detener el cambio. Sin embargo, aparte de los asientos, los caprichos de la moda todavía permiten muchas opciones en la elección de la superficie, y algunas de ellas cuentan con PVC. Una solución que da una sensación de "lujo" voluminosa al tiempo que conserva una buena resistencia a la abrasión y un buen rendimiento de estiramiento es el PVC sólido sobre una tela de respaldo de fibra de poliéster no tejida. Para obtener propiedades de absorción de energía reales, a diferencia del "tacto suave", la espuma flexible de poliuretano proporciona la mejor respuesta. Cada vez más, la espuma PUR se aplica con el tejido de la cara y el forro en una sola operación, como un trilaminado con una capa de espuma de hasta 20 mm de espesor. El PVC es demasiado versátil para desaparecer por completo de la escena. La lámina de PVC/ABS, respaldada por espuma PUR semirrígida, sigue siendo la superficie más utilizada para los paneles de instrumentos. Más recientemente, el PVC se ha mezclado con PUR para proporcionar superficies más resistentes a la temperatura.
Textura
Los acabados texturizados y granulados son populares tanto para molduras duras como blandas. (Esto es quizás una suerte, porque el granulado es una forma eficaz de disfrazar defectos e inconsistencias en una superficie). Con PVC en sus diversas combinaciones, el "acabado de cuero" se produce durante el calandrado. La elección del grano puede ser más crítica con ABS y PP moldeados por inyección. Los granos excesivamente finos se desgastan fácilmente, al igual que los pequeños "granos" que resultan de la superficie de una herramienta pulida con chorro de arena. Tal daño produce un efecto brillante muy obvio en una superficie por lo demás uniformemente mate. La combinación de colores se ve fácilmente afectada por el alisado involuntario de las superficies mate. Ciertos colores oscuros son particularmente susceptibles. Hacer coincidir los paneles adyacentes puede ser un procedimiento muy complicado cuando se trata de diferentes grados y diferentes acabados de grano.
Nebulización
La nebulización es ahora un tema de gran interés. Ha surgido preocupación debido a la emisión de vapores de composición incierta en el dominio de los pasajeros, así como a la condensación de los vapores menos volátiles en las ventanas. El problema ha existido desde que las pinturas de nitrocelulosa, los acabados de cuero y los plastificantes de PVC volátiles contribuyeron a lo que fue ampliamente admirado como el "olor a automóvil nuevo". El olor de los autos nuevos de hoy puede ser menos agradable, pero sin duda es más saludable. El empañamiento está asociado con un ajuste suave; los ingredientes principales son plastificantes de PVC volátiles (ahora reemplazados por plastificantes poliméricos) y productos resultantes de la interacción entre PU y PVC. Sin embargo, también se han identificado lubricantes y retardadores de llama. El área más grande son las fundas de los asientos, pero debido a su temperatura, el panel de instrumentos se ha identificado como la fuente principal. También contribuyen los elastómeros de las alfombrillas, juntas y polainas. Aunque los interiores de los automóviles modernos experimentan un cambio de aire varias veces por minuto, el empañamiento es un fenómeno muy visible y se considera un peligro potencial para la salud. El asunto está recibiendo ahora una atención generalizada. En Alemania hay una prueba oficial de nebulización (DIN 75 201), y desde 1987 se ha realizado mucho trabajo de investigación.
Panel de instrumentos (IP) o tablero
La IP o el tablero de instrumentos encarna muchas funciones en el automóvil moderno, desde contribuir a la integridad estructural del vehículo hasta proporcionar atractivo para las ventas. El tablero es vital ya que alberga una serie de componentes como velocímetro, indicador de combustible, tacómetro, odómetro, sistema de control de clima y características de seguridad como carcasas de bolsas de aire. Las direcciones IP se pueden clasificar como paneles táctiles o suaves. Los paneles Hardtouch se utilizan en automóviles de gran volumen como base para la fabricación de IPs integrados y/o módulos de cabina, de modo que puedan soportar bolsas de aire y proporcionar una funcionalidad básica. Por el contrario, los paneles de tacto suave constan de un componente estructural a nivel de la base con una viga transversal integrada y espumas o almohadillas de choque que absorben los impactos.
Sin aminas
Los sistemas PUR son necesarios para evitar los efectos interactivos que podrían ocurrir con los compuestos de PVC/PUR a altas temperaturas. Debido a su mejor resistencia a la temperatura, el PUR está apareciendo cada vez más en la imagen, incluso hasta el punto de un sistema completo de polímero único en PUR, con una espuma de piel integral, recubierta en el molde con pintura PUR, y todo apoyado sobre una base en llanta estructural PUR. La fascia moldeada por inyección en mPPO es en gran parte autoportante, adquiriendo integridad estructural a partir de su forma profundamente contorneada. Además, la moldura recibe un tacto suave y una superficie menos resonante mediante una capa gruesa de pintura PUR rellena. Los paneles de instrumentos presentan una imagen cambiante, donde la única certeza es un cambio mayor. Las tendencias hacia un montaje más barato y temperaturas más altas son definitivas; las incertidumbres son los factores de "moda" como la textura y la dureza. Otros paneles sensibles a los impactos Ninguno de los otros paneles que forman el interior del automóvil es tan complejo y crítico como el panel de instrumentos; algunos son poco más que separadores de espacios, cuyas principales características son visuales y táctiles. Entre estos dos límites hay varios paneles con claros requisitos de resistencia. Básicamente, se dividen en dos grupos:
- Paneles donde la resiliencia y la tenacidad son la característica principal
- Paneles donde la rigidez es importante además de la resistencia al impacto
Están representados por las clases D y A, respectivamente, en la figura 4.4. La primera categoría incluye piezas que podrían impactar al conductor en una colisión, como las cubiertas de los pilares "B" y la parte inferior del panel de instrumentos, y sus paneles de acabado adyacentes. El ABS no reforzado y una variedad de copolímeros de PP se utilizan comúnmente para estos componentes. Los mismos materiales resistentes y resistentes se utilizan para los componentes que necesitan protección de los pies de los pasajeros (cenefas de los asientos, placas de protección) o de sus palos de golf (forros de botas). Los tiradores de puerta también suelen estar moldeados a partir de copolímeros de PP sin modificar. La segunda categoría comprende lo que son partes esencialmente estructurales, como las bandejas de los asientos traseros y los respaldos de los asientos traseros que se pliegan para formar parte del piso de carga. La aplicación más exigente de esta clase es, por supuesto, el suelo de carga en sí. Es más probable que las especificaciones para estas piezas se basen en la resistencia a la flexión en lugar de la resistencia al impacto. El refuerzo de fibra de vidrio es la característica común: el PP reforzado con fibra de vidrio moldeado por inyección se usa para las bandejas de los asientos, pero es más probable que los pisos de carga exijan la resistencia adicional y la resistencia a la deformación del refuerzo de la estera de vidrio. La matriz puede ser termoestable o termoplástica; es decir, poliéster insaturado o polipropileno. Paneles donde la resiliencia y la tenacidad son la característica principal. Paneles donde la rigidez es importante además de la resistencia al impacto.
Paneles de moldura diversos
El área donde el polipropileno ha hecho más incursiones en las aplicaciones de ABS "tradicionales" es el área general muy extensa de paneles que no requieren una gran resistencia o elasticidad, ni una apariencia de alto brillo. Las principales necesidades son una superficie granulada bien reproducida, con buena resistencia a la abrasión y retención del color. Desde el advenimiento de los grados de reología controlada, estos atributos han ido acompañados de una buena estabilidad de forma y ausencia de distorsiones. Un grado típico será un copolímero de PP que incorpore un 30% de talco. Cuando se requiera una rigidez adicional, como en bitácoras de instrumentos o soportes para bandejas de paquetes, se puede usar un grado de talco al 40% basado en homopolímero. Los copolímeros con un 20% de talco son adecuados cuando se necesita más resiliencia, como en el interior de la guantera, los adornos laterales y las cubiertas de los pilares "A" y "C". El ABS todavía se usa para muchos paneles de esta categoría, en particular consolas y paneles laterales. Las alternativas de mayor costo al ABS en paneles de alta visibilidad, como los revestimientos de pilares, son mezclas como ABS / PC y mPPO. Los paneles con acabado textil continúan estando a favor, especialmente para paneles de puertas y bandejas para paquetes. La celulosa impregnada de resina (aglomerado) y la lámina de PP rellena de madera son los materiales más populares para estos prensados de bajo contorno, cubiertos con poliéster tejido o de punto, y aún, ocasionalmente, con PVC expandido. Los revestimientos de techo constituyen un caso especial, con problemas únicos. El diseño básico ampliamente utilizado de una hoja preformada de cartón resinado, adherida sobre toda la superficie, no es realmente adecuado para los clientes actuales ni para las técnicas de producción actuales. Las tendencias apuntan a una instalación más fácil y una superficie más lujosa y suave. Por lo tanto, se utilizan cada vez más tejidos de punto con respaldo de espuma de diversos tipos, aunque todavía existe un mercado importante para el PVC expandido. Una nueva solución de bajo costo es una composición de moldeo que comprende vellón de fibra textil unida con resina fenólica. Acústica Hoy en día el ruido es una consideración muy destacada.
Acústica
Hoy en día el ruido es una consideración muy destacada. Al igual que otras "comodidades" como la calidez, la amortiguación y el aire fresco, las expectativas del público viajero con respecto a la tranquilidad se vuelven más exigentes año tras año. Se ha logrado mucho en la reducción del ruido del viento, el ruido de la carretera y el ruido del motor; en consecuencia, los pequeños chirridos y traqueteos que emanan de las piezas de plástico que constituyen el revestimiento interior son ahora mucho más notorios. Los automóviles pequeños generalmente necesitan una suspensión más firme para minimizar los cambios en el manejo debido al nivel de carga; como resultado, son más propensos a las vibraciones. Las mejoras en el rendimiento acústico primario, en términos de amortiguación del sonido transmitido por el aire y por la estructura, se pueden atribuir principalmente al poliuretano. Las espumas PUR flexibles se utilizan para el aislamiento del mamparo del motor, la bandeja del piso, el techo y las puertas. Normalmente, la espuma flexible se intercalará entre el panel estructural y una "masa trasera", en forma de una capa pesada de PVC o poliolefina rellena de minerales. Los modelos recientes, cuentan con espuma PUR inyectada en las secciones huecas de la estructura de la carrocería y el panel de instrumentos. Las características acústicas secundarias (es decir, los chirridos y traqueteos) se atribuyen al movimiento entre pares de componentes plásticos. Los efectos son sensibles a la temperatura y la humedad y son extremadamente difíciles de rastrear. La lubricación y la mezcla de materiales son generalmente útiles y es importante que los sujetadores de las molduras retengan suficiente torque con respecto a la temperatura y la fatiga. También son relevantes las variaciones en la rugosidad y la presión de contacto. El PP es claramente mejor que el ABS en todo el rango de frecuencias, en términos de amortiguación del sonido transmitido por la estructura, pero en términos del sonido transmitido por el aire, la diferencia es mucho menor. El revestimiento textil tiene un pequeño efecto beneficioso, pero el acabado de la superficie tiene una influencia insignificante. Todo el tema, debido a su gran conocimiento de los clientes, está atrayendo una cantidad considerable de investigación científica.
Componentes estructurales y mecánicos
Las estructuras de los asientos de fijación son el área de los interiores de los automóviles donde los plásticos han hecho menos incursiones. La construcción de asientos ha sido reconocida durante mucho tiempo como uno de los elementos más laboriosos en la producción de un automóvil, por lo que la motivación para simplificar drásticamente el proceso de ensamblaje es clara. Sin embargo, los muy altos costos involucrados en el diseño y la prueba de estructuras completamente nuevas, en materiales que generalmente no se aceptan como "estructurales", han sido un poderoso impedimento. A principios de la década de 1980 se presentaron varios asientos conceptuales totalmente de plástico: uno basado en nailon reforzado con vidrio y otro basado en polipropileno reforzado con vidrio. Un asiento de autobús urbano de este material ha sido utilizado (con una especificación más simple) desde 1982. No se intentó comercializar las ideas para automóviles de pasajeros en ese momento. En un clima de mayor conciencia de seguridad, la atención se centró en los asientos traseros, que tienden a presentar un conjunto de problemas bastante menos complejos. Los respaldos de los asientos traseros y los pisos de carga se vienen desarrollando en los EE. UU. Una de las primeras aplicaciones de este sistema en Europa fue en el automóvil familiar de la serie T en 1986. Aquí se seleccionó el sistema GMT-PP después de comparaciones exhaustivas con SMC y con acero y aluminio. Utilizando un diseño con dos carcasas soldadas electromagnéticamente, los sistemas de plástico mostraron un ahorro de peso del 40% en comparación con el acero y el aluminio, junto con importantes ahorros de costos. El dispositivo de dividir asimétricamente el asiento trasero también es relativamente más fácil de lograr en una estructura de plástico. Dentro de las opciones de plásticos, se prefirió PP GMT a SMC debido a un menor peso y un mecanismo de falla menos drástico. Las ventajas de los estampados de estera de vidrio sobre las molduras de inyección de fibra de vidrio corta en pisos de carga de área grande son bastante claras; el modo de falla es de agrietamiento progresivo más que desintegración catastrófica. Tradicionalmente, las bandejas de asiento sólidas se consideraban inferiores a los marcos con resorte de celosía. Las mejoras en la tecnología del poliuretano, como las espumas de doble dureza, han transformado la situación. Una vez que la base sólida del asiento se volvió aceptable, era inevitable que el acero fuera reemplazado por uno u otro material plástico. El asiento trasero asimétrico de 1989 presenta dos bandejas de PP reforzado con vidrio moldeado por inyección, con una variedad de opciones de revestimiento textil. Han seguido otras versiones sobre este tema, especialmente en PP-GMT. La espuma de doble dureza se moldeó directamente en la cubierta textil, revestida con una película de barrera, con los accesorios ya colocados para ensamblar dentro de la carcasa de ABS. De hecho, los nuevos diseños de asientos en producción todavía se deben más a los desarrollos en la tecnología de espuma PUR que al diseño estructural. Los asientos del Renault Twingo, fabricados con nuevas técnicas de espuma en tela sin barreras, son un buen ejemplo de esto. Los componentes críticos, el respaldo y el bastidor auxiliar, están fabricados en nailon 6 reforzado con vidrio 30% modificado contra impactos. Es un material de alta resistencia, pero como todos los plásticos reforzados tiene un bajo alargamiento para romperse, lo que implica falla por fractura en lugar de deformación. Este problema fue superado por el diseño de amortiguadores especiales, hechos en una mezcla de PC/ABS con características muy uniformes en el rango de temperatura relevante. La propia carcasa del asiento es de ABS. Este concepto de asiento sobrevivió a la prueba de impacto trasero de 50 km/h (que había fallado en muchos otros asientos de plástico), y se informó que cumplía totalmente con los requisitos de ECE R17, R21 y R25, y con el FMVSS 201, 202 y 207 estadounidense. Se ha demostrado de forma concluyente la eficacia de las estructuras totalmente plásticas. Hay muchos materiales compuestos con la capacidad probada de funcionar como armazones de asientos, respaldos y bandejas. Sin embargo, aún deben abordarse cuestiones de ingeniería de producción, rentabilidad y confiabilidad. La creciente intrusión del reciclaje en el debate está destacando el estatus especial de S-RIM, ya que ofrece la posibilidad de una única solución de polímero, que cubre tanto la estructura como el relleno.
Climatización HVAC
Hace cuarenta años, las instalaciones para el control del medio ambiente dentro del habitáculo de los coches europeos eran rudimentarias, y para muchos modelos básicos incluso un calefactor era un extra opcional. Por supuesto, la transformación al nivel actual de sofisticación ha sido impulsada por la competencia y la demanda de los consumidores, pero los plásticos la han facilitado en gran medida. Desde su aparición a principios de la década de 1960, el polipropileno se ha utilizado como "divisor de espacio" relativamente barato. Su capacidad para producirse en formas complicadas, mediante moldeo por inyección o moldeo por soplado, lo hacía muy adecuado para conductos de calefacción "enterrados" detrás del tablero, siendo más compacto y económico en espacio que los tubos de PVC corrugado. Los calentadores y acondicionadores de aire son estructuras muy similares. El componente más grande es la carcasa, y el PP se ha convertido en la opción más rentable, generalmente como dos molduras rellenas de talco engrapadas o atornilladas. En el interior, los intercambiadores de calor son de aluminio con tanques de extremo de nailon reforzado con vidrio, muy al estilo de los radiadores de refrigeración. Las turbinas y el ventilador suelen ser de acetal o PP reforzado con vidrio y los mandos que forman parte del cuadro de instrumentos, de ABS. El acero (más confiablemente plano en secciones delgadas) generalmente se retiene para las solapas, respaldado con espuma de PUR. Las rejillas para desempañar el parabrisas, componentes muy largos que requieren baja contracción y buen flujo de fusión, ahora se están fabricando en SMA modificado con caucho. Muebles de puertas y ventanas En épocas anteriores, las manijas de las puertas interiores y las ventanillas solían ser piezas de fundición de aleación de zinc cromado. Su tamaño, forma y ubicación podrían volverlos bastante letales en una situación de colisión, y se ha ejercido un ingenio considerable en el diseño de sistemas más efectivos y eficientes, con accesorios más seguros en la interfaz del pasajero. Se ha hecho un buen uso de la capacidad de rendimiento y la libertad de diseño de los plásticos de ingeniería. Los mangos se encuentran con mayor frecuencia en nailon sin relleno, que ofrece el equilibrio óptimo entre rigidez y dureza, pero ocasionalmente en acetal, para brindar mejores características de adherencia y deslizamiento. Los diseños de cerraduras de puertas exigen una combinación de rigidez y dureza extremas; de ahí que intervengan nailon reforzado con vidrio y algunos elastómeros termoplásticos muy flexibles, así como nailon sin relleno y acetal. Los sistemas de cierre centralizados controlados eléctricamente han creado una demanda de mecanismos fiables de bajo ruido. Los diseños de ventanas quizás hayan progresado aún más. Los sistemas de cinta controlados a distancia proporcionan un producto mucho más fácil de usar, ya que utilizan acetal para el soporte de la ventana y el bloque de transmisión y la mayoría de las partes móviles. Las carcasas del motor son normalmente de nailon reforzado con vidrio. Convertir la velocidad del motor a una velocidad aceptablemente baja de movimiento de la ventana implica un mecanismo de transmisión complejo. Se han desarrollado productos especiales a base de nailon con lubricantes internos para los engranajes reductores necesarios.
Volantes
Tradicionalmente, el volante se compone de un esqueleto metálico cubierto de plástico. Durante unos 40 años, el recubrimiento fue butirato de acetato de celulosa (CAB); duro, resistente a los arañazos y resbaladizo en climas cálidos. El aumento de la conciencia de seguridad llevó al cubo abombado y al sobremoldeo en PP y PVC. Más recientemente, al cumplir con los requisitos de ECE 21 y FMVSS 203, se ha logrado un rendimiento mejorado frente a los requisitos de impacto en la cabeza y el cuerpo mediante el uso de espuma PUR de revestimiento integral para cubiertas de ruedas y relleno de bujes. Los proveedores de materiales y los fabricantes de motores han realizado un gran esfuerzo para diseñar volantes con estructura de plástico. La dificultad es que el producto debe mostrar una alta rigidez y una buena resistencia a las vibraciones junto con un modo de falla dúctil. Es poco probable que algún material pueda cumplir con todos estos requisitos. Los híbridos pueden ser la mejor respuesta, por ejemplo, utilizando un cubo de metal combinado con radios y ruedas de nailon reforzado. BASF ha producido un híbrido compuesto por una llanta hecha de éster de vinilo reforzado con filamento enrollado y buje y radios moldeados de nailon reforzado endurecido. Otros diseños aparentemente exitosos consisten completamente en nailon moldeado por inyección, reforzado con fibra larga o reforzado con fibra corta endurecida. Claramente, tanto el costo como los factores de seguridad deberán examinarse en profundidad antes de que se establezcan los volantes de plástico en las series de automóviles de gran volumen.
Bolsas de aire
Las actitudes hacia el principio de las bolsas de aire y las opiniones sobre su aceptabilidad aún varían de un mercado a otro. Ni los diseños ni el papel de los plásticos en ellos se han cristalizado hasta ahora. Sin embargo, es interesante una breve revisión de los materiales utilizados en el primer sistema de airbag europeo, introducido en el Porsche 944 en 1987: el propio airbag era de nailon tejido, con una capa de clorobutadieno ignífuga. La entrada de gas se reforzó con poliéster PBT. Los sensores comprendían un resorte de cobre-berilio y tres molduras de polieterimida ensambladas con adhesivo epoxi. Los cables que unen los sensores con la unidad de diagnóstico estaban revestidos de PVC, con tapones de extremo moldeados en nailon, PBT o caucho de nitrilo. Las bobinas de contacto, que trasladan la señal a la cápsula de gas, se alojaron en PC. El sistema de cubo y dentado de la bobina estaba hecho de acetal y PTFE, con un dispositivo de centrado en un polímero de injerto ABS. La carcasa de la toma de la píldora de encendido era de nailon 6 reforzado con vidrio, con tapas de sacrificio de nailon 6 sin relleno. La cubierta ('puerta de despliegue') del módulo del controlador era una moldura S-RIM PUR, incorporando una malla de nailon de refuerzo y sostenida un cinturón de tela de aramida. El módulo de pasajeros era similar pero con un marco de metal espumado en la cubierta. Se compatibilizó en el tablero con una lámina de aluminio cubierta con espuma de PUR y lámina de ABS, que se abrió con bisagras a medida que se inflaba la bolsa de aire. Este ensayo de materiales fue una especie de tributo a la versatilidad de los plásticos. Los diseños posteriores se han vuelto más simples.
Cinturones de seguridad
La llegada del airbag no reemplaza en modo alguno al cinturón de seguridad, que sigue siendo cualquiera que sea el nivel de impacto. Los diseños actuales de cinturones de seguridad están bien establecidos; las correas en sí son de nailon tejido o poliéster, y los sistemas de inercia y las fijaciones son combinaciones de molduras de nailon, PET y acetal (¡pero sin excluir el acero!), lo que proporciona una rigidez, resistencia al impacto y rendimiento de fricción óptimos. Los sistemas de retracción y los ajustadores de altura más sofisticados han llevado a un uso aún mayor de termoplásticos de ingeniería.
Pedals
Plastics hizo una breve pero exitosa entrada en el área de los pedales de control a principios de la década de 1960, cuando varios modelos de General Motors estaban equipados con pedales de acelerador montados en el piso en molduras de polipropileno que incorporan una bisagra integral. Estos representaron una reducción de costos de dos tercios en comparación con el equivalente de acero y caucho. Más recientemente, se han establecido diseños en voladizo de pedales de embrague y acelerador en plástico. El nailon reforzado con vidrio es la clase preferida de material, estando las molduras cerradas para utilizar la orientación de la fibra para maximizar la resistencia del componente. La resistencia del material es más que adecuada, aunque es necesario diseñar alrededor de su bajo alargamiento para romperse utilizando una sección muy acanalada. Tal sección de nailon reforzado con vidrio superará a una sección en U de acero (que tenderá a abrirse bajo carga de flexión) y también dará una reducción de peso del 30%. Los pedales de este tipo fueron introducidos en 1991. Prevalece una precaución comprensible con respecto a los pedales de freno. Sin embargo, se ha demostrado que se puede lograr una fiabilidad total en un pedal de freno de plástico. El modelo de 1989 presentaba un pedal de freno en nailon reforzado con vidrio. El material era nailon 66 moldeado por inyección que incorpora un 50% de fibras de vidrio largas. La carga de fatiga en un rango de temperaturas con cargas de hasta 900 kg no dejó ninguna impresión en estos pedales después de un millón de ciclos. El diseño y la selección de materiales son factores de suma importancia en estos componentes críticos. También se necesitan cifras convincentes de costo-beneficio y confiabilidad antes de que los plásticos puedan ser generalmente aceptados en estos componentes en automóviles de volumen. Puede ser necesario considerar subconjuntos completos que incorporen un marco de plástico reforzado, así como los pedales.
Instrumentos
Las superficies de las lentes curvas no reflectantes son molduras de PMMA, los controles de ventilación están principalmente en ABS y es probable que las carcasas de los interruptores sean de nailon o PC. Los interruptores táctiles de membrana ahora también están comenzando a aparecer, con membranas en película de poliéster. Los respaldos y carcasas de los instrumentos están moldeados en ABS o PP relleno de mineral. El ABS tiene la ventaja de poder ensamblarse fácilmente con las lentes acrílicas mediante soldadura con placa caliente, pero el PP ofrece ventajas en cuanto a costos y versatilidad. La industria automotriz todavía atiende al fumador, aunque con menos generosidad que en los días de los ceniceros montados en la puerta y en el respaldo del asiento. La nueva tecnología está representada por los forros de poliimida que ahora se utilizan en los forros de puros. Los ceniceros (¡aquí elevados a la categoría de instrumentos!) Se han fabricado tradicionalmente con compuestos fenólicos. En los últimos años, sin embargo, se han utilizado versiones retardantes de llama de nailon en Francia y España, para dar una superficie frontal que podría combinarse con el color del resto del panel de instrumentos.
Hard trim
Las superficies rígidas que se encuentran con mayor frecuencia en los interiores de los automóviles se basan en ABS y polipropileno. El ABS se ha establecido durante mucho tiempo en molduras duras en virtud de su tenacidad, rigidez y resistencia al rayado, su rendimiento dimensional confiable basado en su baja contracción del molde y su agradable apariencia de brillo medio. Sin embargo, el ABS sigue siendo el preferido para muchas piezas sensibles a la apariencia y dimensionalmente críticas, particularmente en formulaciones mates. A un precio ligeramente más alto, las mezclas de PC / ABS ofrecen una combinación bastante mejor de resistencia a la distorsión por calor y estabilidad dimensional que ABS o PP.
Paneles de acabado varios
El área donde el polipropileno ha hecho más incursiones en las aplicaciones de ABS 'tradicionales' es el área general muy extensa de paneles que no requieren gran resistencia o elasticidad, ni apariencia de alto brillo. Las principales necesidades son una superficie granulada bien reproducida, con buena resistencia a la abrasión y retención del color. Desde el advenimiento de los grados de reología controlada, estos atributos han ido acompañados de una buena estabilidad de forma y ausencia de distorsiones. Un grado típico será un copolímero de PP que incorpore un 30% de talco (clase C). Cuando se requiera una rigidez adicional, como en bitácoras de instrumentos o soportes de bandejas para paquetes, se puede usar un grado de talco al 40% basado en homopolímero. Los copolímeros con un 20% de talco son adecuados cuando se necesita más resiliencia, como en el interior de la guantera, las molduras laterales y las cubiertas de los pilares 'A' y 'C'. El ABS todavía se utiliza para muchos paneles de esta categoría, en particular las consolas y los paneles laterales (consulte la figura 4.8). Las alternativas de mayor costo al ABS en paneles de alta visibilidad, como los revestimientos de pilares, son mezclas como ABS/PC y mPPO. Los paneles con acabado textil continúan estando a favor, especialmente para paneles de puertas y bandejas para paquetes. La celulosa impregnada de resina (aglomerado) y la lámina de PP rellena de madera son los materiales más populares para estos prensados de bajo contorno, cubiertos con poliéster tejido o de punto, y aún, ocasionalmente, con PVC expandido. Los revestimientos de techo constituyen un caso especial, con problemas únicos. El diseño básico ampliamente utilizado de una hoja preformada de cartón resinado, adherida sobre toda la superficie, no es realmente adecuado para los clientes actuales ni para las técnicas de producción actuales. Las tendencias apuntan hacia una instalación más fácil y una superficie más lujosa y suave. Por lo tanto, se utilizan cada vez más tejidos de punto con respaldo de espuma de diversos tipos, aunque todavía existe un mercado importante para el PVC expandido. Una nueva solución de bajo costo es una composición de moldeo que comprende vellón de fibra textil unida con resina fenólica.
Otras aplicaciones
Los plásticos están ahora presentes en todos los componentes funcionales del interior del automóvil. Los mecanismos de cambio de marchas, los controles del freno de mano y los interruptores y ajustadores de la columna de dirección proporcionan muy buenos ejemplos de "híbridos", en los que los plásticos y los metales trabajan juntos con el máximo efecto. Se utiliza PTFE (¡rentable!) Para evitar problemas de pegado y deslizamiento en los controles y articulaciones de las bisagras de los pedales. El tema general es que los plásticos proporcionan las formas de precisión y las superficies de fricción, con varillas o placas de acero que proporcionan rigidez a bajo costo. Todas estas aplicaciones son un terreno fértil para los plásticos de ingeniería: el nailon, relleno y sin relleno, es el caballo de batalla, seguido del acetal y el PBT. Muchos de los métodos de ensamblaje rápido de hoy en día dependen de sujetadores de "un solo viaje" ingeniosamente diseñados, generalmente moldeados en nailon 66. Igualmente omnipresentes son los diversos clips de ajuste del mismo material, diseñados para un ensamblaje y desmontaje rápidos. La gama funcional de plásticos se ha ampliado con compuestos de nailon reforzados con fibras largas. Se introdujo la primera aplicación automotriz para esta clase de material en 1987, con una placa selectora de cambios que requería una gran rigidez debido a su gran área sin apoyo. Le siguieron otras aplicaciones, como brazos de visera parasol y brazos de control para espejos exteriores. Estos son componentes menores, pero significativos porque debido a la mayor rigidez en comparación con el nailon reforzado convencional, ha sido posible reemplazar el acero con ventajas de costo y peso.
_________________________________________________________________________________________________________________
Consola central
La consola central está hecha con nuestro XBLEND B 3000, su densidad reducida y menor peso, equilibrio rigidez-tenacidad, resistencia al calor, adherencia mejorada a componentes blandos. Este nuevo ABS/PC también ofrece una ventaja de costos en comparación con el PC/ABS tradicional. La densidad reducida, el alto flujo y las ventajas de costo del ABS/PC para esta aplicación.
El marco de la consola central (de inglés Center console frame) se puede producir en PC/ABS o usando un nuevo material: XLEND AP (ASA/PA). Es posible crear una estética innovadora para versiones de color claro y oscuro, brindando una superficie mate, resistencia a los rayones, estabilidad a los rayos UV, fácil flujo y resistencia a alto impacto.
Rejilla de altavoz se compone de mezclas de ABS con poliamida (ABS/PA), POM o ABS. ABS/PA combina una excelente resistencia al impacto y resistencia química con un alto flujo de fusión y una buena amortiguación acústica. ABS/PA es especialmente adecuado para acabado de superficie mate.
La guantera ( de inglés Glove box) está fabricada con nuestra XBLEND B 3000, su densidad reducida y menor peso, equilibrio rigidez-tenacidad, resistencia al calor, adherencia mejorada a componentes blandos. Requiere absorción de alta energía durante el impacto frontal, buena adherencia a la espuma de PU y alta estabilidad dimensional, la densidad reducida, el alto flujo y las ventajas de costo del ABS / PC para esta aplicación.
Nuestro ABS (XSTIR B 4040) es optimizado para molduras interiores de automóviles, como reposabrazos, molduras de asientos e instalaciones de maletero, XSTIR B 4040 ABS tiene un grado de emisiones muy bajo. Su alta fluidez y resistencia al calor media lo hacen adecuado para aplicaciones de paredes delgadas debajo de la línea de la puerta. Caracterizado por una alta resistencia al calor y una fuerte resistencia al impacto, XSTIR B 4040 es un grado ABS de bajas emisiones diseñado para molduras interiores automotrices utilizadas en la parte superior del automóvil, incluidos rollos de puertas, molduras de puertas, material de revestimiento de puertas y consolas centrales.
Durable, impermeable, a prueba de polvo; hecho in polipropileno o copoliestere (TPC-ET), diseño especial con manchas antideslizantes y agradables al tacto. Marcable por impresión láser, tampográfica o serigráfica. Evite que el polvo y los objetos pequeños caigan en el orificio del enchufe.
La carcasa del espejo retrovisor interior está moldeada con un material que se mezcla con los otros materiales acabados de la cabina. Normalmente sería un homopolímero de polipropileno o una moldura de ABS. Solo se refuerzan las partes estructurales. En la mayoría de los automóviles, los espejos de vidrio interiores convencionales han sido reemplazados por espejos de policarbonato.
Materiales: XBLEND B 3000
Propiedades peculiares: Resistencia al calor, resistencia al impacto, baja emisión, excelente apariencia estética, resistencia al rayado, flexibilidad
_______________________________________________________________________________________________________________________________________________________
Marco de la consola central
Materiales: XBLEND AP (ASA/PA)
Propiedades: Color claro y oscuro, superficie mate, resistencia a los rayones, estabilidad a los rayos UV, fácil flujo, resistencia a alto impacto.
_______________________________________________________________________________________________________________________________________________________
Rejilla de altavoz
Materiales:
- ABS o ABS/PA, POM
Propriedades: No requiera pintura, colorable, mate o brilloso, metalizable
_______________________________________________________________________________________________________________________________________________________
GuanteraMaterial: XBLEND B 3000
Propiedades: Equilibrio rigidez-tenacidad, resistencia al calor, adherencia mejorada a componentes blandos, absorción de alta energía durante el impacto frontal, buena adherencia a la espuma de PU, alta estabilidad dimensional, la densidad reducida.
______________________________________________________________________________________________________________________________________________________
Pastilla de pedal de freno
Este producto está fabricado con TPV de alta calidad para servirle durante muchos años. Diseñado con tecnología de punta y pensando en los clientes, este producto durará toda la vida. Satisfará sus necesidades y ofrecerá una gran calidad a un precio asequible.
Materiales:
- TPV (XPRENE V A55 NEGRO) PP/EPDM Vulcanizado
- SEBS (XPREN EB 60A NEGRO)
Propiedades: Baja emisión, resistencia química, excelente apariencia estética, resistencia ala abrasion, flexibilidad
_______________________________________________________________________________________________________________________________________________________
Clips (sujetadores)
Dependiendo de sus usos previstos, los sujetadores automotrices generalmente están hechos de acero inoxidable o plástico. Los sujetadores de plástico no son tan fuertes como los de acero inoxidable, pero tienen una resistencia bastante alta a los golpes y vibraciones, y pueden ser más adecuados para su uso en la fijación de tapicería y otras aplicaciones no estructurales.
Materiales:
- PA 66 30% FV stabilizada al calor
- PA66 Modificad al impacto stabilizada al calor
- PA66 12% FV stabilizada al calor
Propiedades: Buena elasticidad, alta resistencia al impacto
_______________________________________________________________________________________________________________________________________________________
Manija de puerta
Dispositivo interior o exterior para accionar la cerradura de las puertas de los vehículos, a fin de permitir su cierre y su apertura. La manija exterior, ya desde sus primeras aplicaciones, ha conservado durante mucho tiempo una función práctica, con los exclusivos condicionamientos debidos a los dictados del gusto estético y la coherencia estilística de los accesorios. La clásica palanca horizontal con eje de rotación perpendicular a la puerta fue durante muchos años la única en los coches de serie, debido también al mecanismo sencillo y seguro; todo lo más, los carroceros variaron el estilo de la manija manteniendo el eje horizontal. El cuerpo esta hecho de plástico ABS de alta calidad y la palanca en PA66 con carga mineral, de alta resistencia, duradero en uso. La palanca puede ser pintada con acabado cromado.
Propiedades: anticorrosión, color suave y brillante, larga duración
_______________________________________________________________________________________________________________________________________________________
Tapicería interior
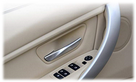
Propiedades: Resistencia al calor, Resistencia al impacto, Fluidez, Baja emisión
_______________________________________________________________________________________________________________________________________________________
Tapón universal para toma de mechero
_______________________________________________________________________________________________________________________________________________________
Espejos interiores
Materiales:
- ABS
Propriedades: No requiera pintura, colorable, mate o brilloso, metalizable
_______________________________________________________________________________________________________________________________________________________